Rubber, that bouncy stuff that your tires and shoes are made from? it’s under threat. From deforestation and disease to climate change and shifting markets, the rubber industry has never been in such a precarious position. More than ever before, companies are noticing and are looking for alternatives to the single species that literally makes this industry.
Natural rubber, or latex, starts as tree sap, that gooey sticky stuff that sometimes leaks out of trees. It comes from the rubber tree (Hevea brasiliensis), a tropical deciduous tree that can grow up to 141 ft.
The rubber tree's sap is transformed into the elastic, water resistant, and insulative material that we know so well. Its versatility has helped create more than 40,000 types of products like tires, medical devices, surgical gloves, clothes, toys, mattresses, and sealing products like gaskets.
The need for rubber alternatives is not new. The first alternatives came from petroleum, and after a century of use we now know there’s a critical need to shift away from this reliance. Today, researchers are focused on alternative plant species for natural rubber as well as biobased and waste-based inputs to create (bio)synthetic rubbers.
Rubber has been growing for 3000+ years
Rubber's history traces back to the Olmec civilization (1200-400 BC). Archaeologists have discovered rubber balls on ancient Olmec sites, and it seems like they were used to play a game. This material was later utilized by the Mayans and Aztecs as well. Aztecs likely mixed the tree sap with morning glory juice to harden the material and make rubber sandals (read more on the recipe recreated by MIT scientists).
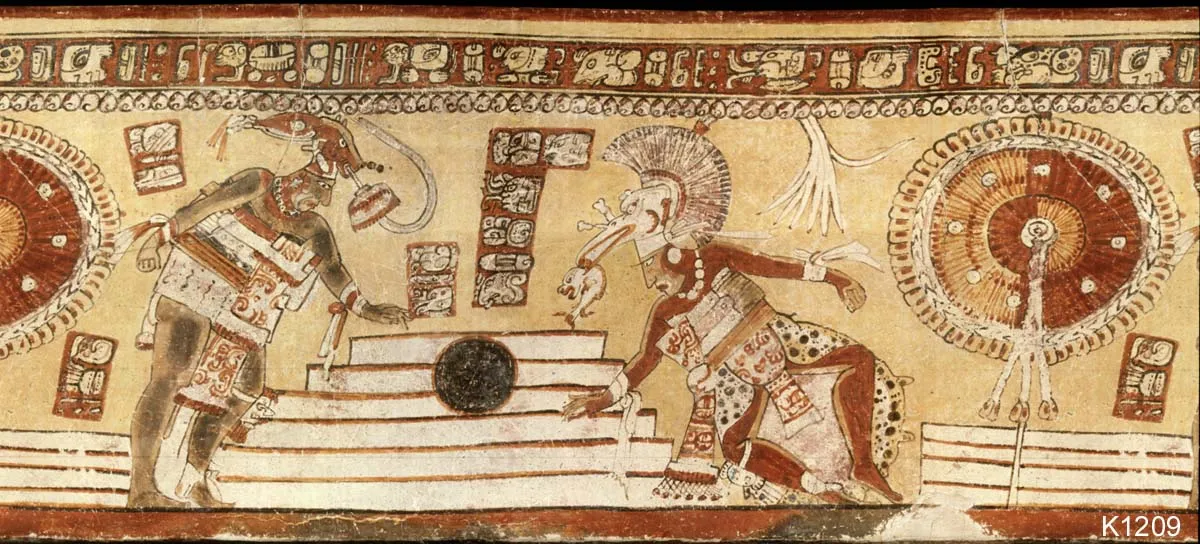
A huge jump in rubber usage began in 1839 when Charles Goodyear accidentally invented vulcanization. This was the next evolution of the Aztec recipe, and included a heating process that made the rubber more durable. It led to the wider use of rubber in things such as car tires, shoe soles, and the many other products that it’s part of today.
The growth of the automobile caused the rubber industry to surge. This demand for tires led to the creation of the first synthetic rubber by Bayer in 1909. The advent of World War II further accelerated synthetic rubber development, with the U.S. manufacturing Styrene-Butadiene to counteract shortages due to the war.
The market saw its next dramatic shift when the 1973 OPEC oil embargo doubled synthetic rubber costs, driving a resurgence in the use of natural rubber, especially for radial tires that required its strength. This resurgence brought natural rubber’s market share up to 39 percent by 1993.
As of 2022, 14 million metric tons of natural rubber were consumed globally with 90 percent produced in Southeast Asia. The tire industry, using 70 percent of the world's natural rubber, remains the largest consumer.
Natural rubber accounts for about half of the rubber produced worldwide. A variety of synthetic rubbers make up the other half of the estimated 29 million metric tons of rubbers produced globally. Synthetic rubbers are often cheaper and have a wider range of performance than natural rubber, but there are still aspects of natural rubber that synthetic rubbers cannot duplicate.
The Rubber Supply Chain Faces Risks from Multiple Fronts
Disease: South American Leaf Blight poses a severe threat to rubber trees. Both organisms thrive in hot, humid regions with abundant rainfall. There have been efforts to contain the disease since 1910, however, these have ended in “miserable failure”. If the Leaf Blight spread to Southeast Asia it would be devastating to the region and could virtually wipe out the industry.
Deforestation: Rubber trees thrive in the rain forests, and their cultivation is a major factor contributing to deforestation. This contributes to loss of biodiversity and to climate change. Convoluted supply chains make it difficult to know if natural rubber is coming from sustainable sources.
Economic and Political Volatility: Market fluctuations and geopolitical tensions can lead to unpredictable supply and pricing. Oil production and trade restrictions can decrease the supply of synthetic rubber, driving natural rubber prices higher. This leads to expansion of rubber plantations, which then drives down prices. That pressure is often felt most directly by workers, who are sometimes forced to work for subminimum wages.
The Future of Rubber is Tree-Free
The recent deforestation regulation (EUDR) in the EU mandates that rubber entering its market be deforestation-free by late 2024. The goal is to enforce supply chain transparency and labor law compliance, currently a major struggle. It’s yet to be seen if the regulation will improve sustainability and labor practices. With virtually all natural rubber coming from the rainforest regions, it’s pretty difficult to grow rubber trees without cutting down at least some forest. This is where alternative organisms can benefit the industry.
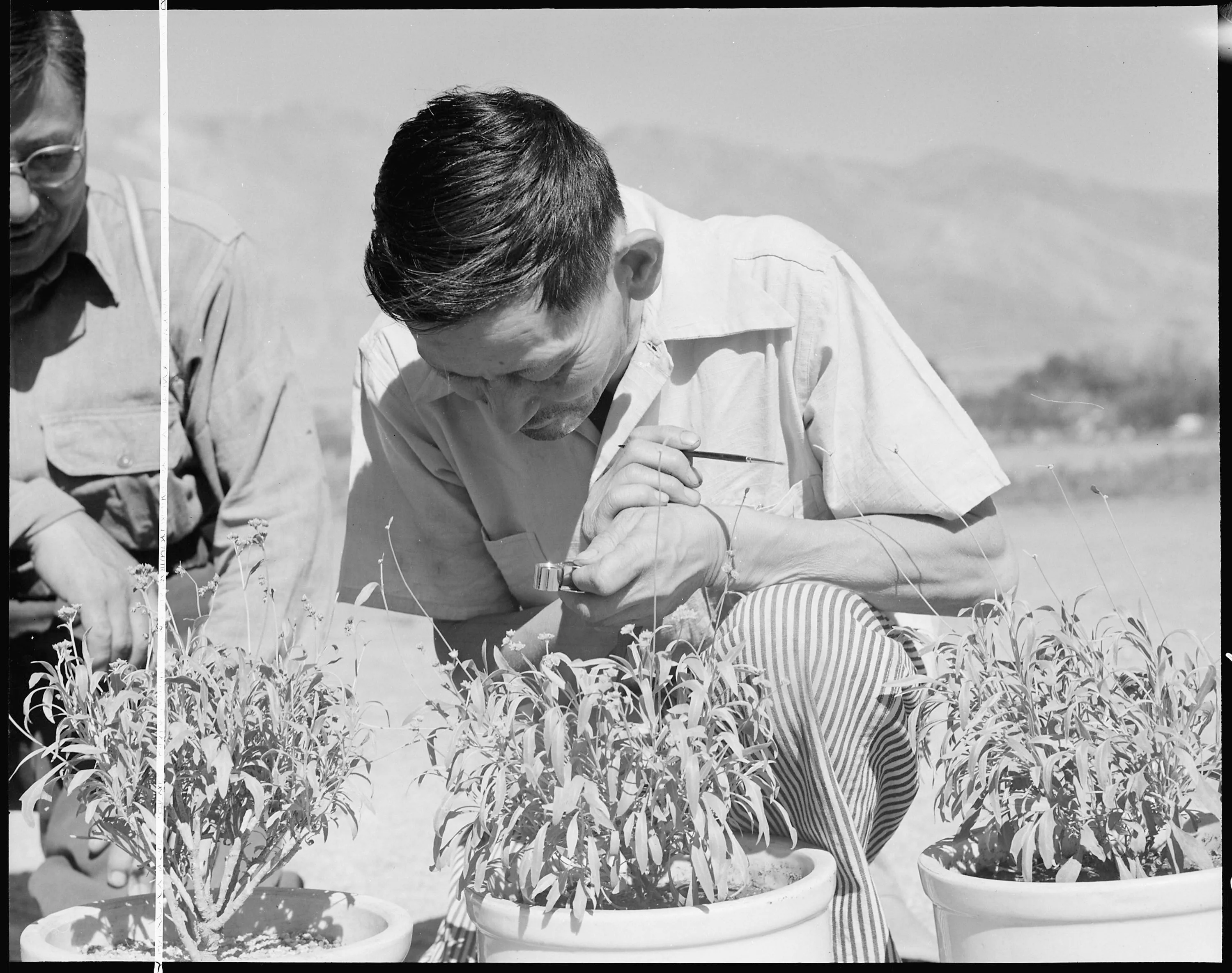
Beyond the Hevea Tree
Ever since the 1920’s when South American Leaf Blight originally decimated the industry, there has been interest in alternatives to the rubber tree. Worldwide shortages were caused by the political tensions leading up to World War II, and then demand skyrocketed because of the war itself. Rubber was a top strategic resource.
Today, for more climate resilience, companies are looking for ways to grow rubber producing plants in cold and arid environments. This also has the potential to slow deforestation from the growth of rubber tree farms in tropical regions.
Another strategy is to create faster growing plants. After a rubber tree is planted it takes 6–10 years before it’s ready to be tapped for latex. Smaller shrubs and annual plants that can be harvested after one season create more flexibility because farmers can simply shift production when demands and prices change.
Rubber from Shrubs
The difficult to pronounce shrub, Guayule can be grown in drought-prone regions and is indigenous to the southwestern US and northern Mexico. Its name comes from the Nahuatl word ulli/olli for rubber.
Guayule was one of the plants that came onto the scene in the 1920’s in response to the South American Leaf Blight and then saw a resurgence during WWII. Though the most notable research didn’t happen at a school, or inside a corporate lab. It happened in a Japanese-American Internment Camp.
Called the Manzanar Guayule Project, the Japanese-American researchers bred plants that were more productive, and created stronger material than rubber trees. The program lasted two years until 1944 when it and the internment camp was shut down.
Decades later in 2008, this plant saw a resurgence when Yulex developed the first allergen free latex products from Guayule. In 2012 they partnered with Patagonia to release their first non-neoprene wetsuit, and in 2016 Patagonia ended their use of neoprene in wetsuits in favor of Yulex materials.
The company Yulex brought this to market with Patagonia’s natural rubber wetsuits.
Bridgestone has also been researching guayule rubber since 2012. Since then they’ve invested over $142 million. They unveiled their first guayule-based tire in 2015. Bridgestone has continued to grow their capabilities in this space and plans to use guayule rubber at a massive scale.
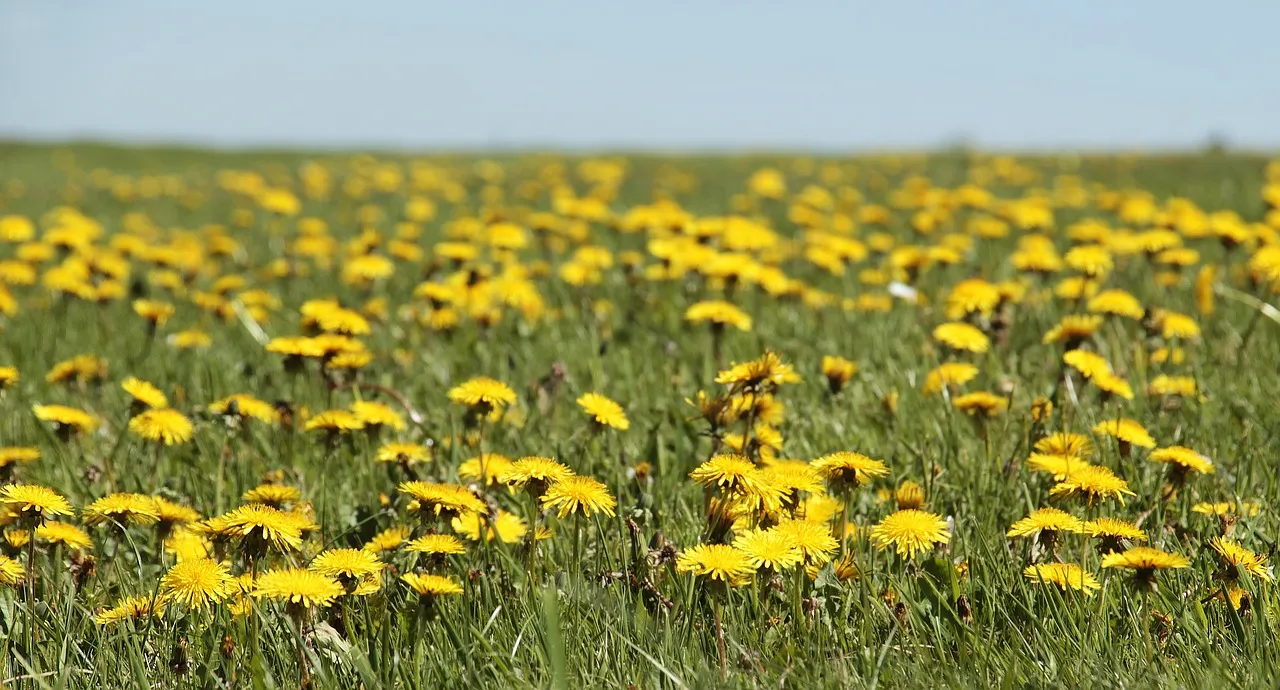
Rubber from Flowers
Dandelion rubber was originally cultivated in the Soviet Union from 1931–1950. It’s derived from the Kazakh Dandelion (Taraxacum kok-saghyz, TKS), and is under renewed development. TKS has a short, six-month harvest cycle compared to the seven-year maturity of rubber trees. It can also be grown outside of the tropics. See how it works in <30 seconds.
Kultevat has been breeding TKS for rubber since 2007 to bring yields up and prices down, with the goal of becoming the leading source of US grown rubber.
Goodyear, in collaboration with the US Department of Defense and the Air Force Research Lab, initiated a program in early 2022 to explore domestic production of dandelion rubber, in partnership with BioMADE and Farmed Materials.
Continental Tire started developing dandelion rubber in 2011. In 2021 they launched Urban Taraxagum as the first dandelion rubber bicycle tire.
Edison Agrosciences is breeding sunflowers for rubber by boosting the amount of natural latex made by the plants. Today US sunflower fields produce 50,000 tons of rubber, yet it’s just too costly to extract. If Edison Agrosciences is successful, then this crop will double as a source of rubber.
All of these alternative plants show the potential for rubber to be produced without total reliance on the rubber tree. From the threat of disease, to the practicality of growing more locally, alternative plants make a lot of sense.
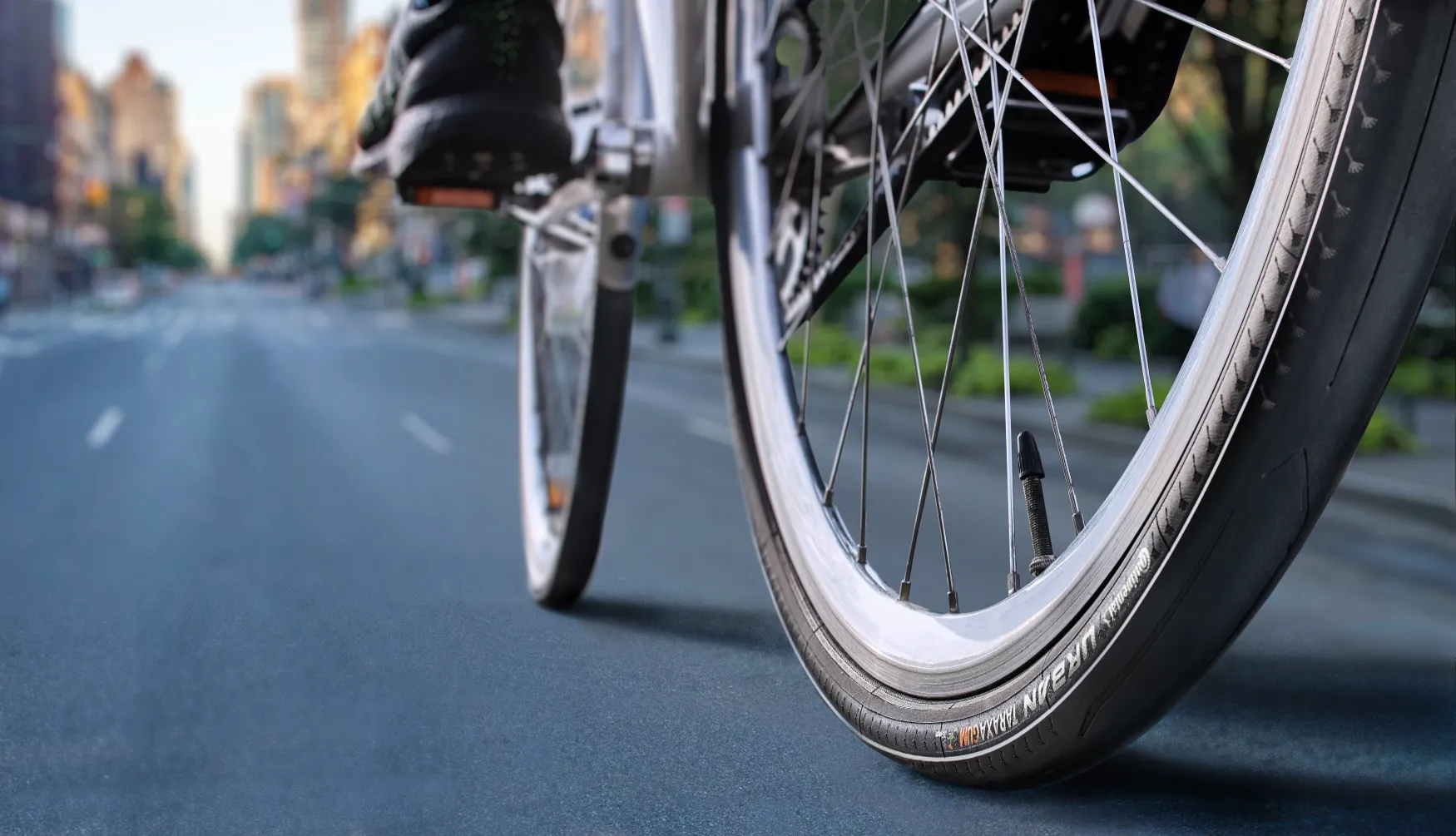
One more company is sourcing a rubber-like compound from birch bark. Reselo AB is using this waste stream from the timber industry and extracting the natural compound that makes birch bark flexible. It's not technically rubber (i.e. isoprene), but from what we hear it's pretty close!
Natural and Synthetic Rubbers Might Be Inextricably Linked
Synthetic rubber and natural rubber are often blended to create high performance materials.
Natural rubber is strong, flexible and resistant to wear and tear. Synthetic rubbers can offer better resistance to temperature, aging, and abrasion than natural rubber, but synthetic rubber is more vulnerable to tearing and tends to have lower tensile strength.
Natural and synthetic rubbers are blended to leverage the strengths of both materials. For instance, the high tensile strength and tear resistance of natural rubber can be combined with the superior temperature and aging resistance of synthetic rubber to create a product that performs well under a variety of conditions.
There are many types of synthetic rubber. The most prevalent and generally used is Styrene-Butadiene. Others include Polyisoprene and Butyl, which are used for tire inner tubes because of their resistance to air diffusion. Nitrile is known for oil resistance, and is used in oil handling hoses, seals, disposable gloves, and grommets.
If synthetic rubbers are essential, then what can we do to improve their sustainability performance?
Synthetic Rubber Redefined
About half of all rubber produced is natural and the other half is synthetic. Each has different properties. The best performance comes from blending natural polyisoprene and synthetic isoprene.
To reduce dependence on petroleum, efforts are underway to increase the proportion of biomaterials in synthetic rubbers. Isoprene, a natural rubber monomer and synthetic rubber precursor usually obtained from crude oil refining, is central to these efforts.
The University of Minnesota is devising a method to produce isoprene from biomass, such as trees and grasses. Additionally, Goodyear and Visolis are working together to generate biosynthetic isoprene from biobased materials, using Visolis’s technology to convert lignocellulosic feedstocks into high-quality isoprene.
LanzaTech is collaborating with Sumitomo Riko Company to recycle rubber, resin, and urethane wastes into isoprene.
Lummus Technology and Synthos S.A. are taking a different approach by working on bio-butadiene technology, which will utilize renewable bio-derived ethanol from corn to produce rubber.
Crafting a Resilient Future
The rubber industry is at a critical juncture, with sustainability and innovation becoming the linchpins for its future. While traditional sources are imperiled, the rise of alternative natural rubbers and more sustainable synthetics offer a future for this indispensable material.
Key to this transformation is the call for greater transparency within the natural rubber sector, coupled with the scalable production of alternative sources. Concurrently, recognizing that synthetic rubbers will remain a staple, it's crucial to innovate alternatives that break away from fossil fuel dependence.
Our collective aim must be a future materials industry that is adaptive and robust, poised to meet the challenges of climate change and fluctuating market demands, and safeguarding resources for future generations.